Black Ceramics (Juodoji keramika)
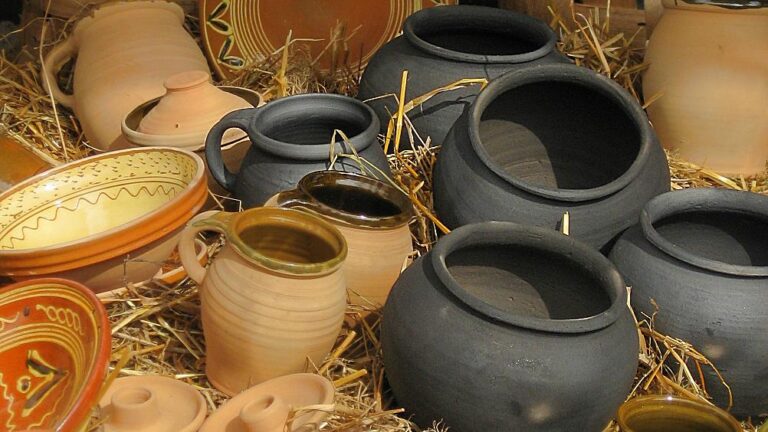
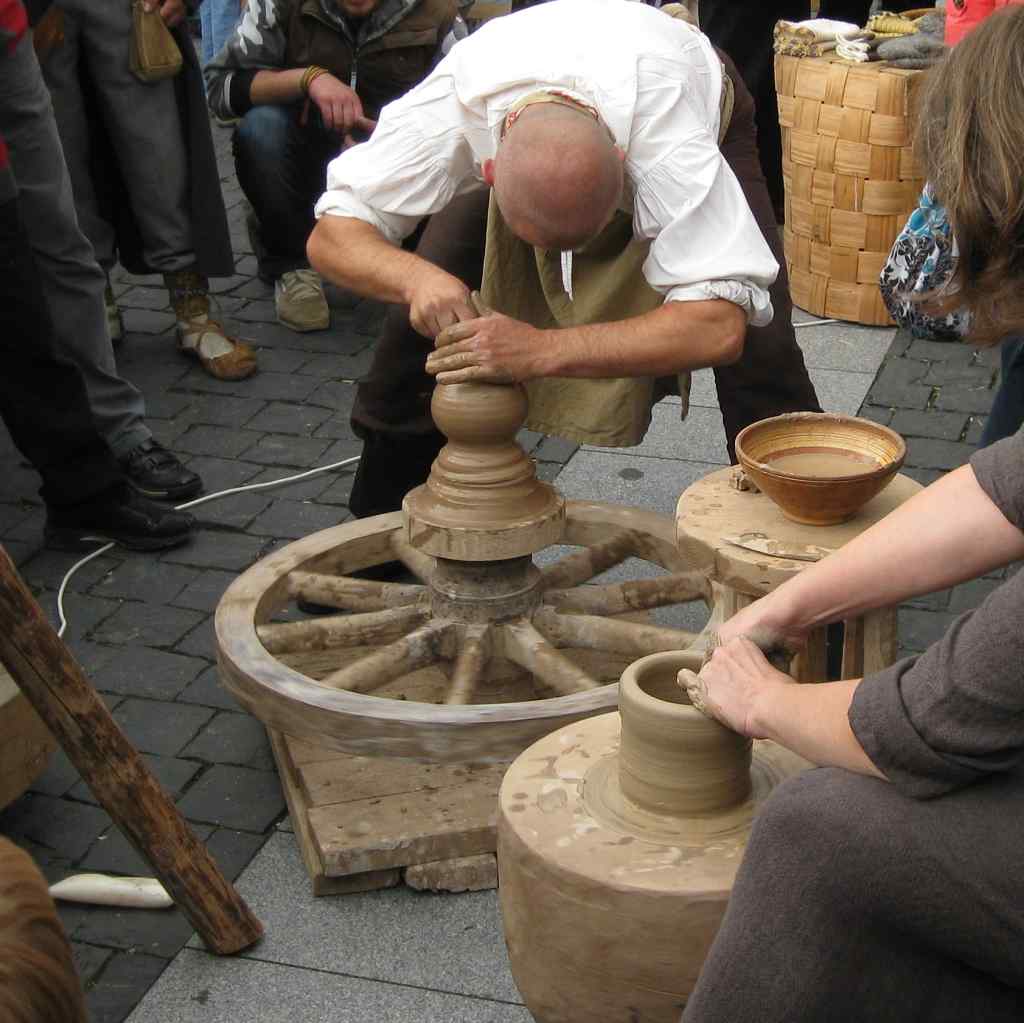
Juodoji keramika
Black ceramics has been practiced in Lithuania for millennia, dating back to the Neolithic era.
According to archeologist Marija Gimbutiene, black pottery was particularly popular in East Prussia (now Lithuania Minor) where it was also used for religious purposes as far back as 4000–2000 BCE. After being cremated, for example, a person’s ashes were put in a special black urn.
Over time, the tradition spread throughout Lithuania, particularly to the region of Dzūkija in the south, where clay-rich soil made pottery production easier. Archeological studies of the Lower Castle of Vilnius proved that in the 14th century black pottery had also spread to this area. Other early pieces of black ceramics in Lithuania are dated to the 16th century, including an ornate pitcher from Kernavė featurning a decorative relief of a hunting scene with dogs and deer (now in the Lithuanian Art Museum in Vilnius).
Most black ceramics, however, were often used for practical purposes in daily life, such as cooking, storage, and transportation of goods. The unique properties of black ceramics, such as their durability, heat resistance, and low porosity, made them particularly well-suited for these practical applications.
Artists use local clay for their creations, ensuring that each piece reflects the culture and environment of the region. This reliance on local materials helps maintain a connection to the land, and the methods are often more sustainable than industrial ceramics production.
One of the most distinct features of Lithuanian black ceramics is the unique firing process. The traditional method, known as pit firing, involves placing pottery in a pit and covering it with organic material like pine needles or wood. As the kiln heats up, the smoke and soot from the organic material penetrate the clay, turning it black and creating a shiny, metallic finish. This technique also makes the pottery durable and water-resistant.
Pit firing, which is the process of firing the pottery in a pit or outdoor kiln using wood and other organic materials as fuel, is particularly important in creating the black color associated with black ceramics. The smoke and ash from the organic materials penetrate the porous surface of the clay during the firing process, leaving behind a dark, smoky color that is characteristic of black ceramics. Basically the pores of the clay have been filled with soot! Without this technique, black ceramics would not have the unique properties and recognizable appearance that makes it so special.
The process of firing a ceramic product takes place in a kiln, often dug or built in the ground. Notice that the unfired pieces are not yet black.
As the temperature is gradually raised, the clay gradually reddens and becomes bright red at 950-1000 °C. Then the kiln is sealed – it is covered with a plate and filled with soil. After reducing the amount of embers, soft (coniferous) firewood or pine needles are thrown into the kiln. They emit thick black smoke. The smoking process continues for up to a day. The smoke closes the pores of the clay and paints the product black and also makes it water tight. The black color is throughout the thickness of the clay.
** Want to learn more about Juodoji keramika?
Become a member of LTFAI.org and get access to our online videos and members area. **
Pottery
Black pottery can be made on a wheel or with a hand-building technique, which involves shaping the clay by hand rather than using a pottery wheel. This technique is preferred for creating unique shapes and designs that may be difficult to achieve using a wheel. These photos are from workshops in Merkinė, Dzūkija and at the Black Ceramics center in Vilnus. Again, notice how the clay iteslf is not actually black before it is fired.
Burnishing involves polishing the surface of the clay with a smooth object like a pebble or bone. There is a specific type called “black-burnished ware” that is from Roman Britain, shown in this image. Burnishing creates a smooth and shiny surface on the pottery and helps to seal the clay, making it more durable and resistant to water. In addition, no paints or glazes are used in the production. All of these advantages are also achieved by the firing techniques used in Lithuania.
Many contemporary artists are not only keeping the tradition alive but are also adapting it for modern times. Through workshops and exhibitions, they are introducing black ceramics to new audiences and helping preserve an important part of Lithuania’s cultural heritage.
Lithuania is one of the few European countries that have preserved the art of black ceramics. Near the Kernavė hill forts, in the forests of Dzūkija around Merkinė, near the Baltic Sea, and in a few other places, you can still find wood burning stone kilns in which wonderful works of art are created, black with glittering with metallic, green, blue, and violet hues.
** Want to learn more about Black Ceramics?
Become a member of LTFAI.org and get access to our online videos and members area. **